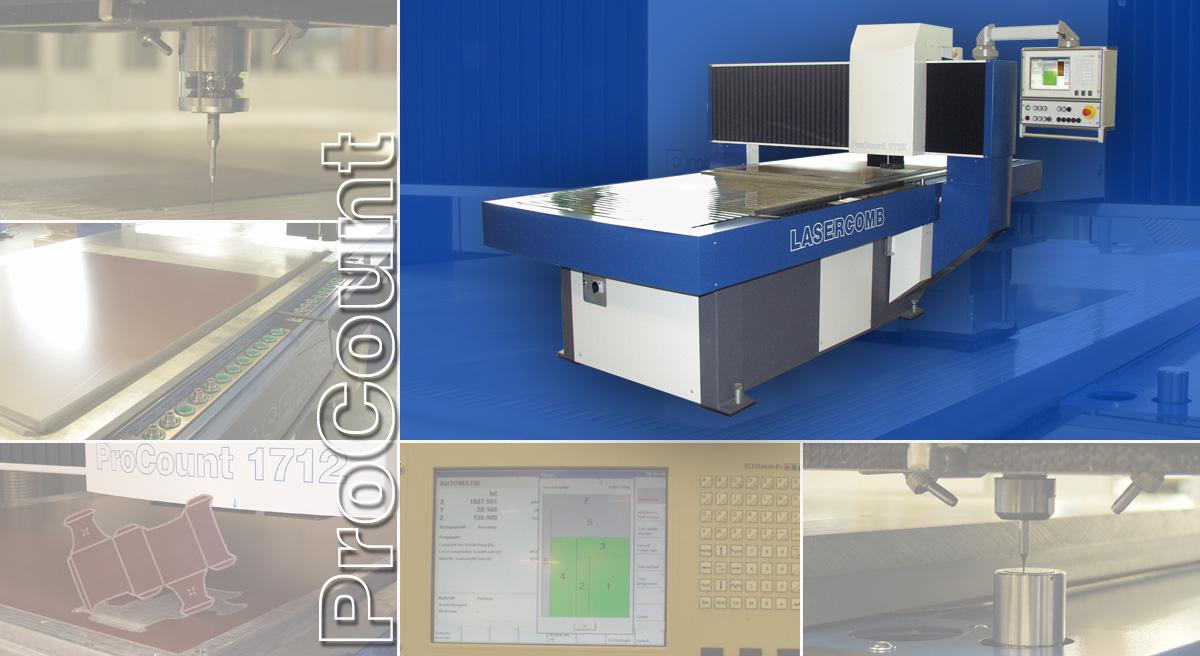
The ProCount system is a high-performing milling machine specifically designed to produce steel counter plates and Pertinax counter plates. A sturdy machine body based on mineral casting in combination with the highly rigid concept of the total machine design grants a minimum of vibrations and favors high precision and productivity.

Operation occurs on a graphic user interface which is comfortable by means of a touch screen and has an intuitive operator guidance. Input of required parameters concerning material and tools is logically and clearly structured. Considerable safety algorithms help to prevent unintentional mistakes. Daily operations are supported by extensive databases and get along with a minimum of input to define the next job and have the machine ready.
The machine is working on the network which allows easy data transmission and besides enables us to support you by remote maintenance.
Speed
Milling feed rate max. 40m/min
Spindle power
6,0 kW
Controlling
CNC for all machine actions
Computer with graphical interface for operation
Options:
Fine mist lubrication
Additional technical features:
- Excellent acceleration and braking performance
- Full-automated measuring of tools
- Tool depot for up to 24 tools
- Free configurable material data base
- Full-automated tool replacement
- Computer controlled working process
- Intelligent layout (I.L.R.)
Our ProCount 1712 system can be adjusted for your requests by means of various additions. There for the following options are available.
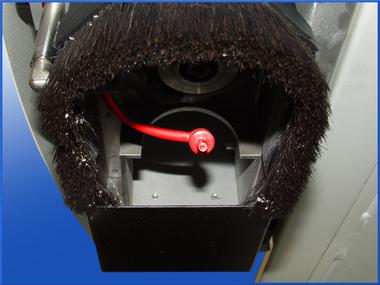
Fine mist lubrication
Minimum amount fine mist lubrication system to score optimal lubrication or rather cooling of tools while milling steel counter plates.
Application: metal processing

Extraction for dry processing
In the standard model an extraction for dry splinters and dust is employed.
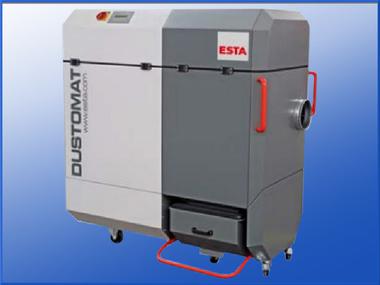
Extraction for moist processing
In combination with the lubrication system an extraction for moist processing is necessary.

Measuring probe
Before every application of the tools the probe measures the tool length, so that tool wear gets detected and adjusted.
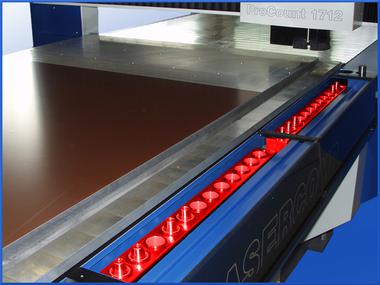
Tool depot
In the standard model a depot with 12 tool places is installed. Optionally, this can be extended up to 24 tool places.

3D infrared sensor
A machine equipped with this sensor head is able to measure dies with cutting and creasing rules inside on exact positions of creases. Also, it is able to measure channel depth. Sensor heads with different shapes and diameter make adjustments for various tasks possible.
The results will be recorded as a measurement report in one file and can be retrieved or printed.